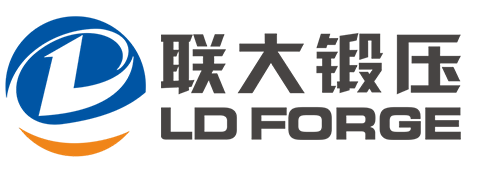
Forging Production
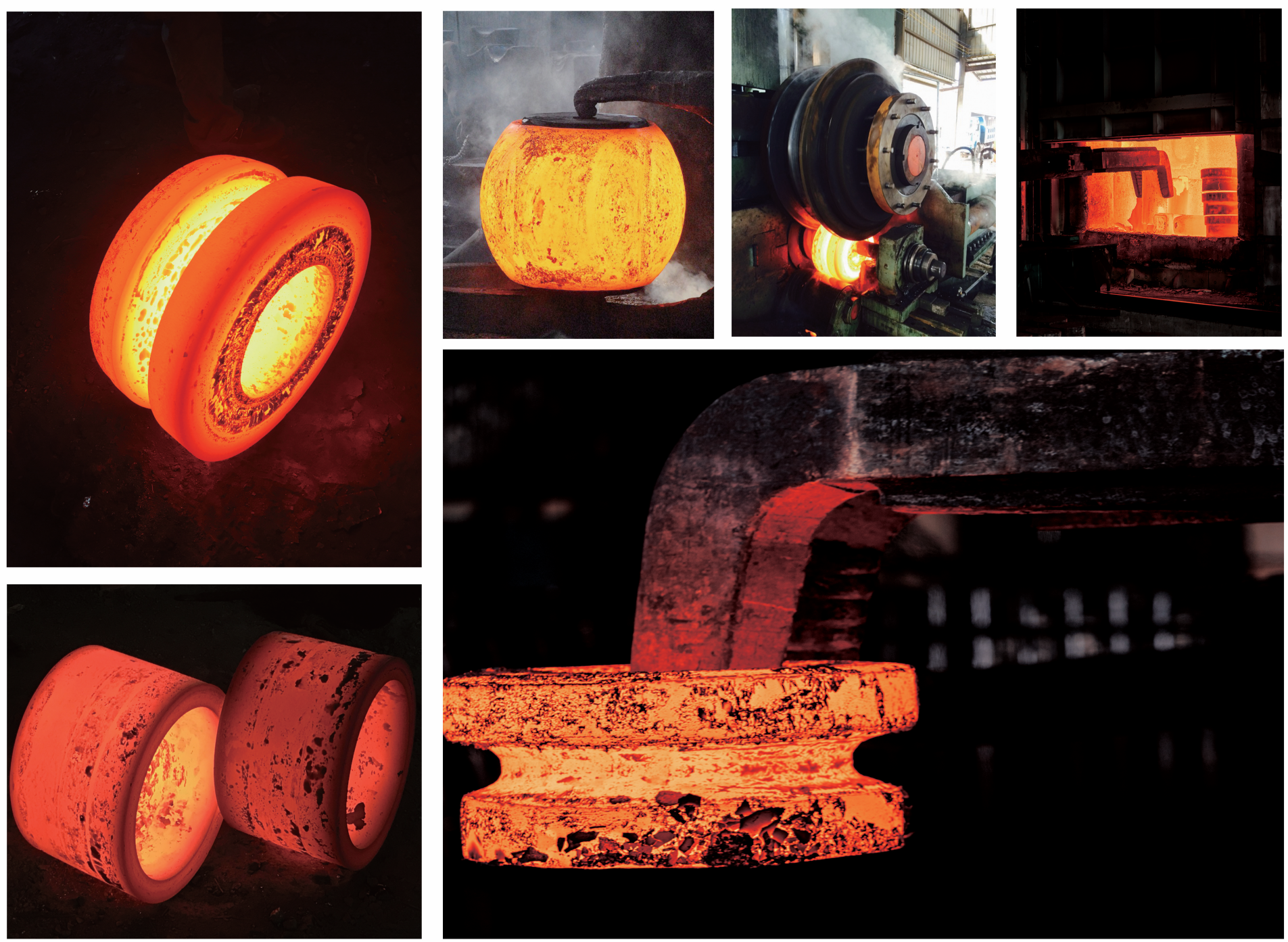
Production Control
LD FORGE production specialists understand the product specifications to find the optimal metal working procedures
for each work-piece, including mould design, material forging properties, forging ratio. Our 30-year experience in the
field of open-die forging and ring rolling tech no logy en ables us to tailor the production procedures to each customer's
special requirements.
Except forging/ring rolling, LD FORGE also provide one-stop service covering in-house machining (rough/finished),
heat treatment (incl. normalizing, annealing, quenching and tempering, solution treatment), metallographic analysis
and NDT (incl・ UT, MT, PT, RT)・ Meanwhile, our continuously「efined production process can meet the strictest product
requirements and offer you more reliable and economic options
/
工业阀门锻造零部件专业制造商
OPEN-DIE FORGING/RING ROLLING MASTER
Forging Flowchart
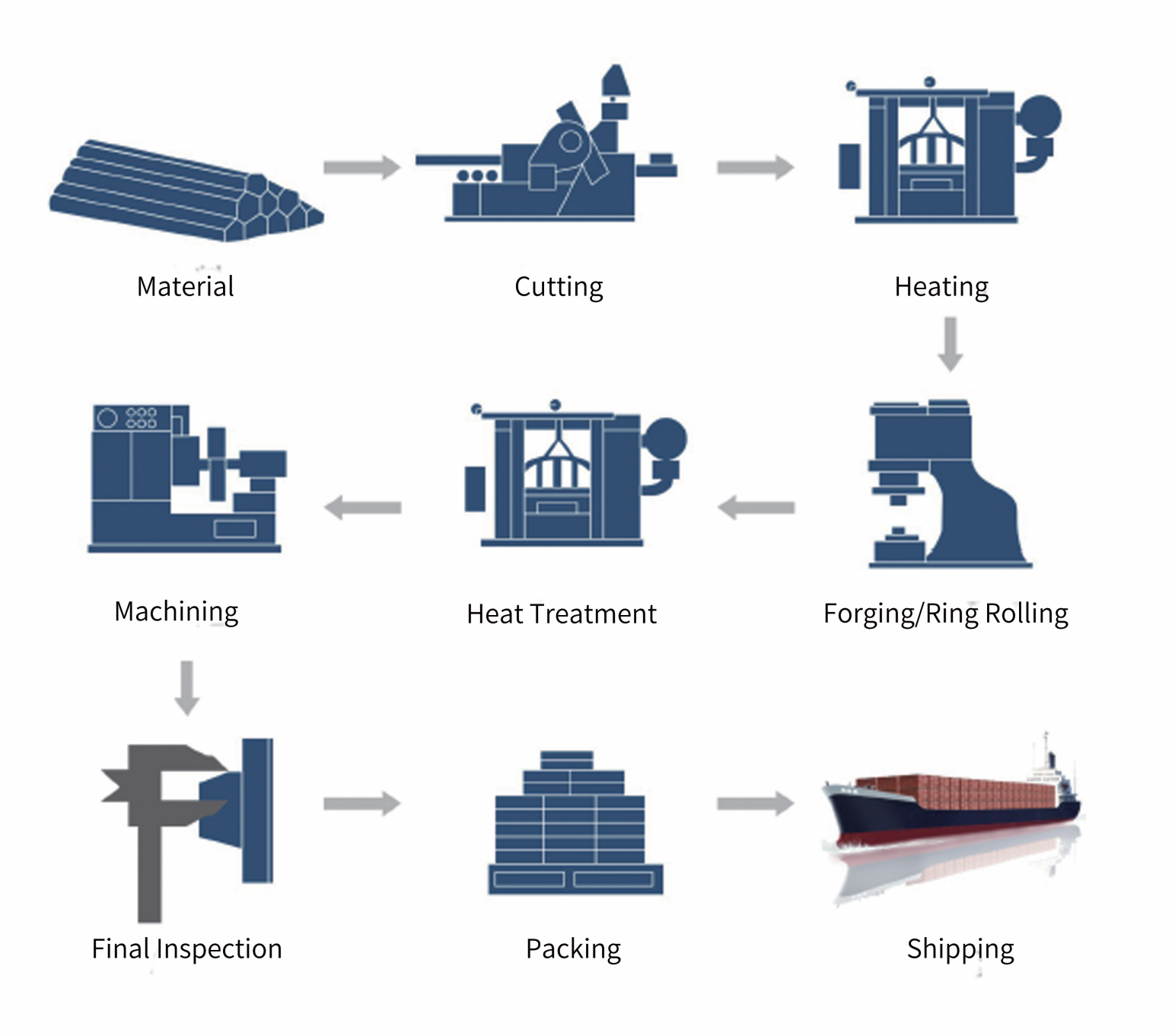
Forging Flowchart
LD FORGE have upgraded two sets of vertical ring rolling mills to manufacture the rolled rings,especially for valvebody (cylindrical hollows forging)from NPS 10"to 36"and valve closures (profiled forgings)from NPS 10"to 24",max outer diameter can reach 1500mm and max height can reach 880mm.
Comparing to traditional hammer forgings,LD FORGE'S ring forgings have much less machining margin benefitedfrom the smooth surface,that can help to reduce the forging weight by max at 30%,as well as the cost.This quickproduction adaption allows us to economically manufacture small quantities as well as large series,which offer ourclients more solutions forthe custom-made forging products.
Forging Flowchart
Customized Combined Mold
Suitable for Forged Ball Valve Closureless than or equal to 10 inch
Closure U-Shape can be Forged
U・Shape of Closure can be Forged Directly,your best cost saving choice
Developed Mold and Design Drawing
Large number of developed mold andready-make closure design drawings